CNC Precision Parts Factory: The Future of Metal Fabrication
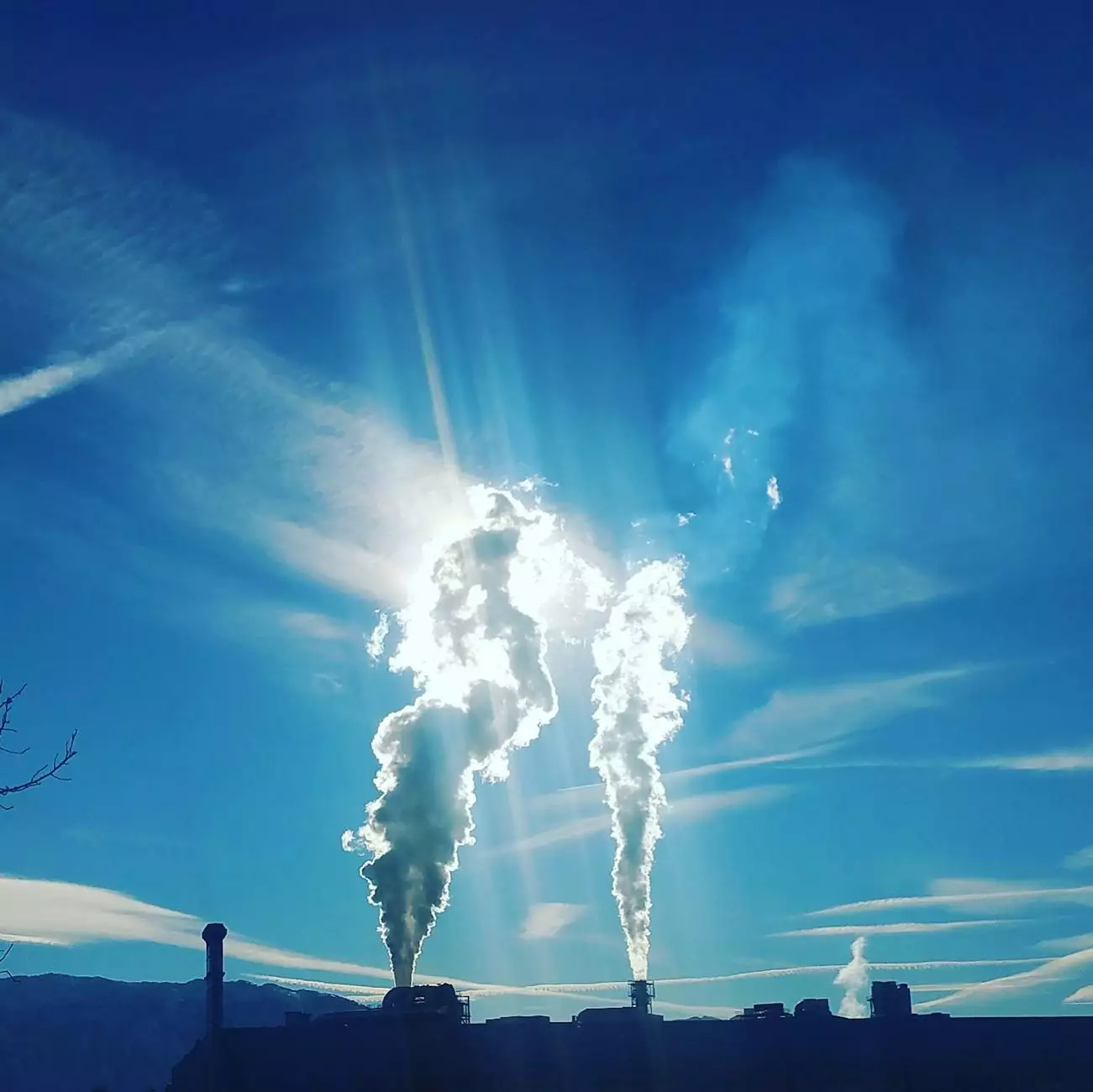
In the realm of manufacturing, CNC precision parts factories play a pivotal role. These specialized facilities utilize cutting-edge technology to create intricate components with remarkable accuracy and efficiency. As industries continue to evolve, the demand for high-quality metal fabrication is on the rise, making a solid understanding of what a CNC precision parts factory offers essential for businesses looking to thrive in competitive markets.
Understanding CNC Precision Parts
CNC, or Computer Numerical Control, refers to the automation of machine tools through the use of computers executing pre-programmed sequences of machine control commands. This technology allows for exacting precision in the manufacturing of parts, reducing waste and improving productivity. The advantages of utilizing a cnc precision parts factory include:
- High Precision: CNC machines are capable of producing intricate parts with tolerances that can be as tight as a few microns.
- Consistency: Once programmed, CNC machines can reproduce the same part repeatedly without variation, ensuring uniform quality.
- Complex Shapes: CNC technology can easily create complex geometries that would be challenging or impossible to achieve with traditional machining methods.
- Reduced Lead Time: The automation involved in CNC machining significantly speeds up production processes, reducing the time from design to delivery.
The Process of CNC Precision Manufacturing
The process of creating precision parts in a CNC precision parts factory involves several stages, each crucial for achieving the final product. Here’s a closer look at these stages:
1. Design and Prototyping
The first step in the CNC manufacturing process is to create a detailed design of the part. This is typically done using CAD (Computer-Aided Design) software. Engineers and designers work closely to ensure that every aspect of the part meets the required specifications and industry standards. Prototyping may also occur at this stage to test the design before mass production.
2. Programming
Once the design is finalized, it is translated into a language that CNC machines can understand. This involves writing a program that dictates the machine movements, speeds, and tools needed to create the part. Skilled machinists utilize specialized software to ensure the program is optimized for efficiency and accuracy.
3. Material Selection
The choice of material is critical in CNC precision manufacturing. Various metals, such as aluminum, steel, titanium, and alloys are commonly used, depending on the desired properties of the final product. The selected material must adhere to the necessary specifications for strength, malleability, and resistance to environmental factors.
4. Machining Process
During the machining process, CNC machines utilize various tools to cut, drill, shape, and finish the materials into the desired form. Techniques such as milling, turning, and EDM (Electrical Discharge Machining) may be employed to achieve complex shapes and features. This stage is where the precision of the CNC process truly shines, as the machines operate with remarkable accuracy.
5. Finishing Touches
After machining, the parts often require additional finishing processes, such as polishing, anodizing, or coating. These finishing touches enhance the aesthetic appeal of the parts, as well as improve their resistance to wear and corrosion. Quality control checks are conducted at this stage to ensure that each part meets the established standards.
Benefits of Partnering with a CNC Precision Parts Factory
Choosing to partner with a cnc precision parts factory offers numerous advantages for businesses in various sectors. Here are several benefits worth considering:
- Expertise and Experience: CNC factories typically employ skilled technicians and engineers who have extensive experience in metal fabrication. Their expertise can help troubleshoot issues and optimize designs for better performance.
- Scalability: CNC precision parts factories can easily scale production up or down based on your specific needs. Whether you require a small batch or a large volume, these factories can accommodate your requests without compromising quality.
- Cost-Effectiveness: While the initial investment in CNC technology may be high, the long-term cost savings due to reduced waste, minimized labor costs, and increased production efficiency make it an economically sound choice for many businesses.
- Advanced Quality Control: CNC precision parts factories often implement rigorous quality control measures throughout the production process. This ensures that every part produced meets the necessary specifications and standards before it reaches the customer.
Applications of CNC Precision Parts
The versatility of CNC milling and turning means that precision parts manufactured in a cnc precision parts factory find applications across a wide range of industries, including:
Aerospace Industry
The aerospace sector demands the highest quality and precision in every component. CNC parts are used in the manufacture of aircraft engines, landing gear, and structural components, where reliability and performance must never be compromised.
Automotive Industry
In the automotive field, CNC precision engineering is employed for parts such as engine components, transmission housings, and intricate brackets. These parts require tight tolerances and durability to ensure optimal vehicle performance.
Medical Devices
Medical technology relies heavily on precision parts for devices such as surgical instruments, implants, and diagnostic equipment. CNC factories produce these components with exceptional cleanliness and precision, adhering to strict regulatory requirements.
Defense and Military
Defense contractors depend on CNC precision parts for a variety of equipment and technologies, from firearms to electronic systems and communication devices. The stringent standards in this sector necessitate uncompromising quality and security.
Trends Shaping the Future of CNC Precision Parts Factories
As technology advances, several trends are influencing the future of CNC precision parts factories:
1. Automation and Robotics
Further automation of manufacturing processes using robotics will enhance efficiency and reduce production times. Robotics can take over repetitive tasks, allowing skilled workers to focus on more complex and creative aspects of manufacturing.
2. Artificial Intelligence
Integrating artificial intelligence into CNC programming and operations can lead to optimization of processes, predictive maintenance, and improved quality control. AI can analyze production data in real-time and adjust processes for maximum productivity.
3. 3D Printing Integration
CNC precision parts factories are beginning to incorporate 3D printing techniques alongside traditional machining practices. This hybrid approach allows for rapid prototyping and the creation of complex geometries that may be difficult to achieve through conventional methods alone.
4. Sustainability Practices
There is a growing emphasis on sustainable manufacturing practices in CNC precision parts factories. This includes sourcing sustainable materials, optimizing energy use in production, and minimizing waste through improved designs and processes.
Finding the Right CNC Precision Parts Factory
When selecting a CNC precision parts factory for your business needs, consider the following factors:
- Capabilities: Ensure that the factory has the equipment and technology necessary to meet your production needs and specifications.
- Quality Standards: Confirm that the factory adheres to industry-standard quality control measures and certifications.
- Experience: Look for a factory with a proven track record of serving clients in your industry, showcasing their expertise and reliability.
- Customer Service: Choose a factory that values communication and responsiveness, as a solid partnership will require collaboration and problem-solving.
The Future of CNC Precision Manufacturing
The future of CNC precision manufacturing looks bright, with continuous advancements in technology and methodology. As industries evolve and the demand for precision parts increases, CNC precision parts factories will be at the forefront of innovation and quality. By leveraging state-of-the-art tools, skilled labor, and best practices, these facilities are well-positioned to meet the ever-growing needs of modern manufacturing.
Conclusion
In conclusion, a cnc precision parts factory represents the pinnacle of metal fabrication, providing unparalleled precision, consistency, and craftsmanship. From the initial design phase to the final product, the meticulous processes and advanced technologies employed in these factories ensure that businesses receive the highest quality components tailored to their specifications. As you consider options for your manufacturing needs, partnering with a trusted CNC precision parts factory could be your key to success in a competitive landscape.